Bearing
Automotive , Energy , Mechanical engineering
Bearing steels are exposed to fatigue and high contact loads. Final hardness can be obtained by through-hardening, case hardening or inductive heat treatment. The most common bearing grades for through-hardening are 100Cr6 families. Those grades combine the advantages of carbon and chromium to achieve heat treatment efficiency and final mechanical properties. Since such grades require annealing before transformation, thermo-mechanical rolling for fine grain size distribution represents an advantage in terms of reducing annealing time.
Steel production requires expertise and strong process control: to achieve high performance, the heat treatment has to be very homogeneous throughout the part. Grade and structure homogeneity is therefore key in order to avoid any segregation during casting or decarburisation in reheating operations.
High fatigue loads require surface quality and low inclusion content. Two metallurgical treatments are available to achieve this. Aluminium killed steel follows a clean metallurgical process to obtain a very low oxygen content. Sillicon killed steel produces grades with good deformability inclusions. The sizes of such inclusions are reduced during the rolling process.
In standard steel production, the reduction ratio is the final process required to enable a fine and homogeneous structure prior to transformation.
The final heat treatment of 100Cr6 grades gives possibilities for either bainitic or martensitic final structure depending on the trade-off required between toughness and hardness. The grade is thus alloyed with molybdenum and/or manganese to favour bainite and/or martensite.
The same considerations on homogeneity and inclusions apply to C55 and C70 for induction hardening
Key properties
Products used
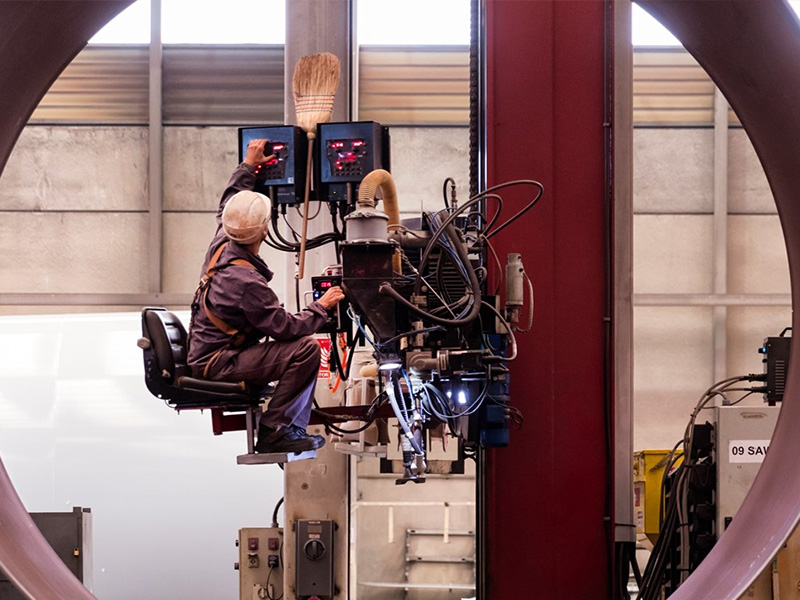
Fatigue life and oxygen content
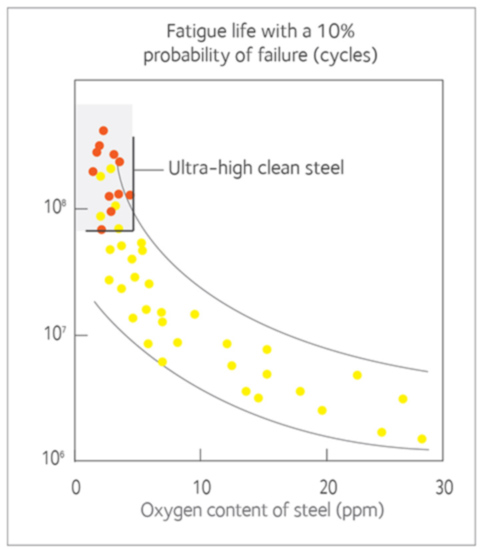
Typical through-hardening bearing steel grade (ISO 683-17)
Material No. | C | Si | Mn | Cr | Mo | |
---|---|---|---|---|---|---|
Name | - | % | % | % | % | % |
100Cr6 | 1.3505 | 1.00 | 0.25 | 0.35 | 1.50 | - |
100CrMo7 | 1.3537 | 1.00 | 0.25 | 0.35 | 1.80 | 0.25 |
Typical induction-hardening bearing steel grade (ISO 683-17)
Material No. | C | Si | Mn | Cr | Mo | |
---|---|---|---|---|---|---|
Name | - | % | % | % | - | - |
C56E2 | 1.1219 | 0.55 | 0.25 | 0.80 | - | - |
C70Mn4 | 1.1244 | 0.75 | 0.25 | 1.00 | - | - |
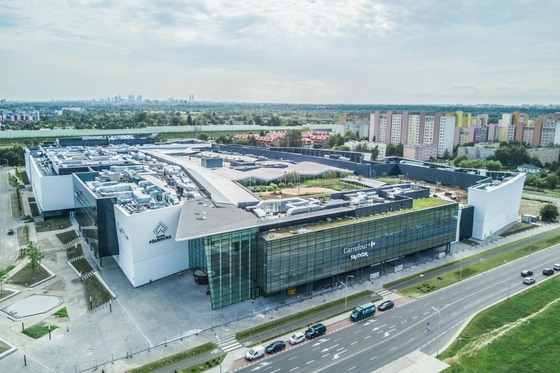