Forging
Automotive , Energy , Mechanical engineering
Carbon and Carbon Manganese Steels
Carbon Steel grades are the most common steels used for forging applications. Low carbon steels (carbon between 0.1 to 0.25%) are the easiest to cold form due to their soft and ductile nature. Medium carbon steels (carbon between 0.26 and 0.59%) are typically used in medium and large parts forgings. High carbon steels (carbon above 0.6 %) are used for applications in which high strength, hardness and wear resistance are necessary, such as wear parts, gear wheels, chains and brackets.
Key properties
Products used
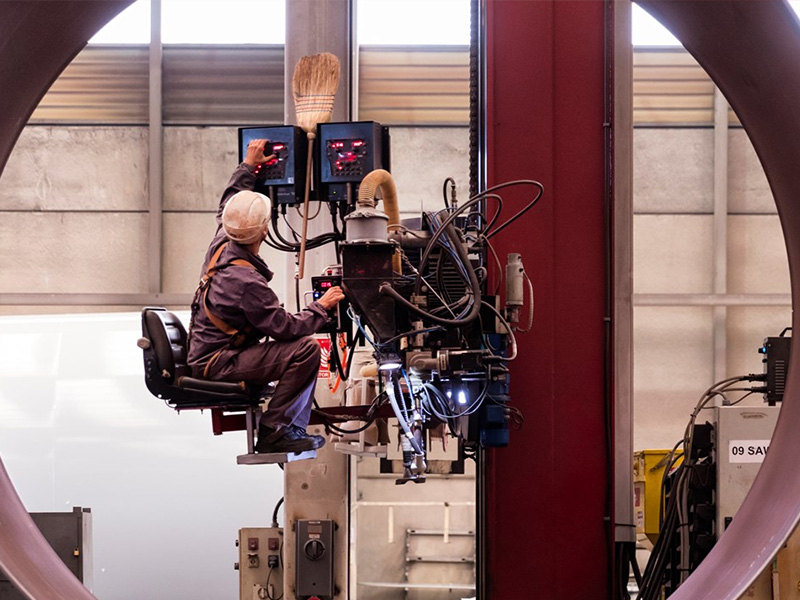
Comparison of mechanical & quenchability properties of AFP, Q+T and bainitic grades
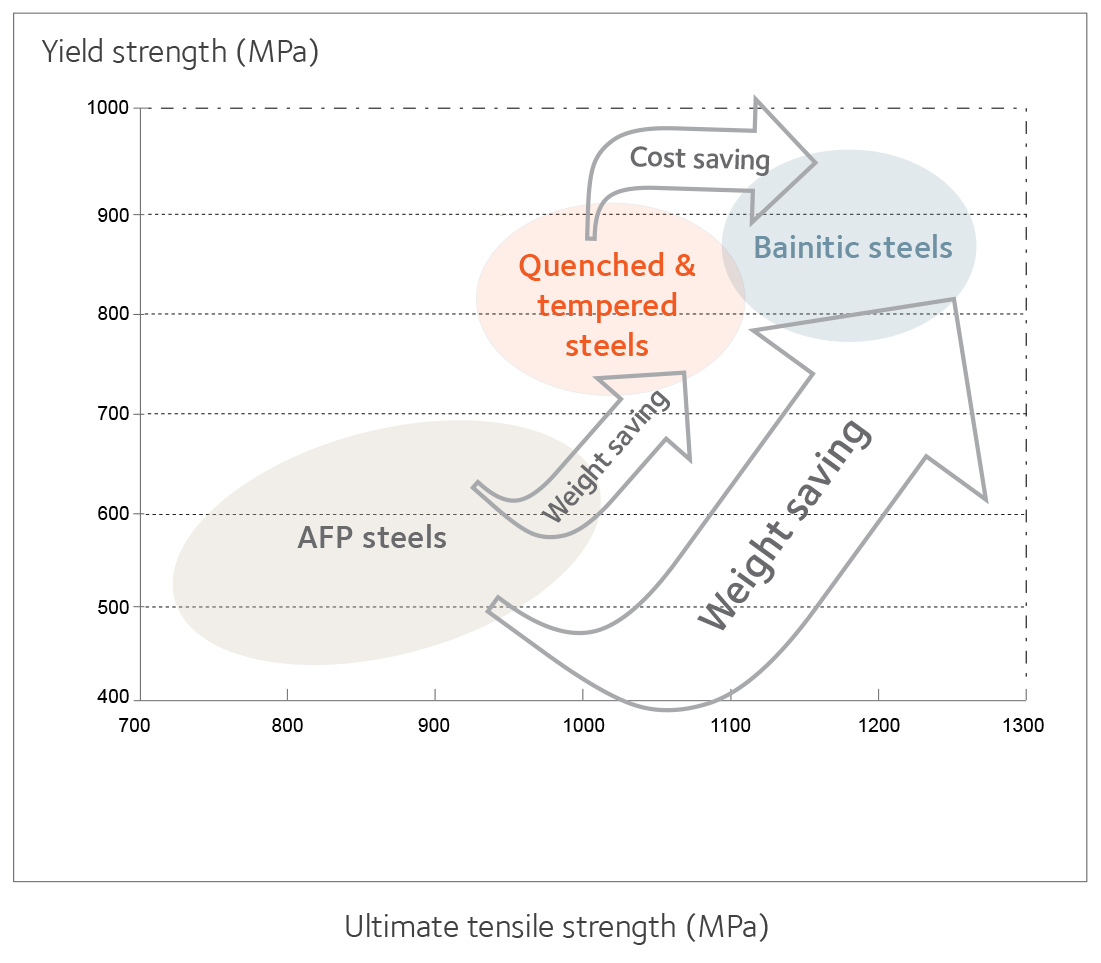
Quenched and tempered steels (Q+T)
Quenched and tempered steel grades are hardenable steels. They are alloyed with chromium and molybdenum for example, to favour transformation of austenite into martensite during the quenching process. The forging part is quenched in water, polymer or oil to obtain the required hardness. The tempering process enables the mechanical properties and toughness to be adjusted.
C | Si | Mn | Cr | Ni | Mo | V | B | ||
---|---|---|---|---|---|---|---|---|---|
Name | Material No. | % | % | % | % | % | % | % | ppm |
25CrMo4 | 1.7218 | 0.22-0.29 | max. 0.40 | 0.60-0.90 | 0.90-1.20 | - | 0.15-0.30 | - | - |
30MnB5 | 1.5531 | 0.27-0.33 | max. 0.40 | 1.15-1.45 | - | - | - | - | 8-50 |
34CrNiMo6 | 1.6582 | 0.30-0.38 | max. 0.40 | 0.50-0.80 | 1.30-1.70 | 1.30-1.70 | 0.15-0.30 | - | - |
38Cr2 | 1.7003 | 0.35-0.42 | max. 0.40 | 0.50-0.80 | 0.40-0.60 | - | - | - | - |
41Cr4 | 1.7035 | 0.38-0.45 | max. 0.40 | 0.60-0.80 | 0.90-1.20 | - | - | - | - |
42CrMo4 | 1.7225 | 0.38-0.45 | max. 0.40 | 0.60-0.90 | 0.90-1.20 | - | 0.15-0.30 | - | - |
C45 | 1.0503 | 0.43-0.50 | max. 0.40 | max. 0.40 | max. 0.40 | max. 0.40 | max. 0.10 | - | - |
50CrMo4 | 1.7228 | 0.46-0.54 | max. 0.40 | 0.60-0.90 | 0.90-1.20 | - | 0.15-0.30 | - | - |
51CrV4 | 1.8159 | 0.47-0.55 | max. 0.40 | 0.70-1.10 | 0.90-1.20 | - | - | 0.10-0.25 | - |
Case hardening steels
Case hardening steels are used for parts that require high surface wear resistance while retaining a soft core that absorbs stresses without cracking. After forging and machining, the outer layer is carburised and/or carbo-nitrided and then locally hardened by quenching. The grades are usually low-carbon steels to which suitable alloying elements have been added. A special characteristic of this kind of grade is the Jominy curve, which needs to be well controlled.
C | Si | Mn | Cr | Mo | Ni | ||
---|---|---|---|---|---|---|---|
Name | Material No. | % | % | % | % | % | % |
C15 | 1.0401 | 0.12-0.10 | max. 0.40 | 0.30-0.80 | - | - | - |
17Cr3 | 1.7016 | 0.14-0.20 | max. 0.40 | 0.60-0.90 | 0.70-1.00 | - | - |
16MnCrS5 | 1.7139 | 0.14-0.19 | max. 0.40 | 1.00-1.30 | 0.80-1.10 | - | - |
18CrNiMo7-6 | 1.6587 | 0.15-0.21 | max. 0.40 | 0.50-0.90 | 1.50-1.80 | 0.25-0.35 | 1.40-1.70 |
20NiCrMo2 | 1.6523 | 0.17-0.23 | max. 0.40 | 0.65-0.95 | 0.35-0.70 | 0.15-0.25 | 0.40-0.70 |
20MnCr5 | 1.7147 | 0.17-0.22 | max. 0.40 | 1.10-1.40 | 1.00-1.30 | - | - |
25MoCr4 | 1.7325 | 0.23-0.29 | max. 0.40 | 0.60-0.90 | 0.40-0.60 | 0.40-0.50 | - |
27CrMo4 | 1.7218 | 0.22-0.29 | max. 0.40 | 0.60-0.90 | 0.90-1.20 | 0.15-0.30 | - |
27MnCr5 | 1.7147 | 0.23-0.29 | max. 0.40 | 1.10-1.40 | 0.80-1.10 | - | - |
Micro-alloyed steel (AFP)
Micro-alloyed steel grades allow the production of parts with higher strength, obtained without subsequent heat-treatment after forging. Typical additions include niobium, vanadium and titanium, which increases yield strength by precipitation hardening, while offering finer grain structures. These two outcomes increase the strength of the forged parts compared to conventional carbon steels.
C | Si | Mn | S | V | N | ||
---|---|---|---|---|---|---|---|
Name | Material No. | % | % | % | % | % | % |
19MnVS6 | 1.1301 | 0.15-0.22 | 0.15-0.80 | 1.20-1.60 | 0.02-0.06 | 0.08-0.20 | 0.01-0.02 |
30MnVS6 | 1.1302 | 0.26-0.33 | 0.15-0.80 | 1.20-1.60 | 0.020-0.060 | 0.08-0.20 | 0.01-0.02 |
38MnVS6 | 1.1303 | 0.34-0.41 | 0.15-0.80 | 1.20-1.60 | 0.020-0.060 | 0.08-0.20 | 0.01-0.02 |
46MnVS6 | 1.1304 | 0.42-0.49 | 0.15-0.80 | 1.20-1.60 | 0.02-0.06 | 0.08-0.20 | 0.01-0.02 |
C70S6 | 0.66-0.73 | 0.15-0.35 | 0.40-0.90 | 0.02-0.07 | max. 0.04 | - |
Bainitic steels
Bainitic steels are designed for applications that require both high properties and process cost reduction compared with Q+T grades. Very high strength can be achieved (UTS > 1100 MPa) without heat treatment: controlled cooling after forging steers the austenite transformation into the bainitic region. The desired level of strength is reached by fine-tuning the alloying elements taking into account the customer's processes and the size of the part. Bainitic steels achieve higher mechanical properties than micro-alloyed grades as well as demonstrating uniform hardness through out the steel.
C | Mn | Cr | UTS | |
---|---|---|---|---|
Designation | % | % | % | % |
Solam® B100 | max. 0.2 | max. 1.9 | max. 1.5 | > 1100 MPa |
Solam® B1150H | max. 0.4 | max. 1.8 | max. 0.8 | > 1150 MPa |
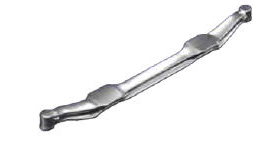
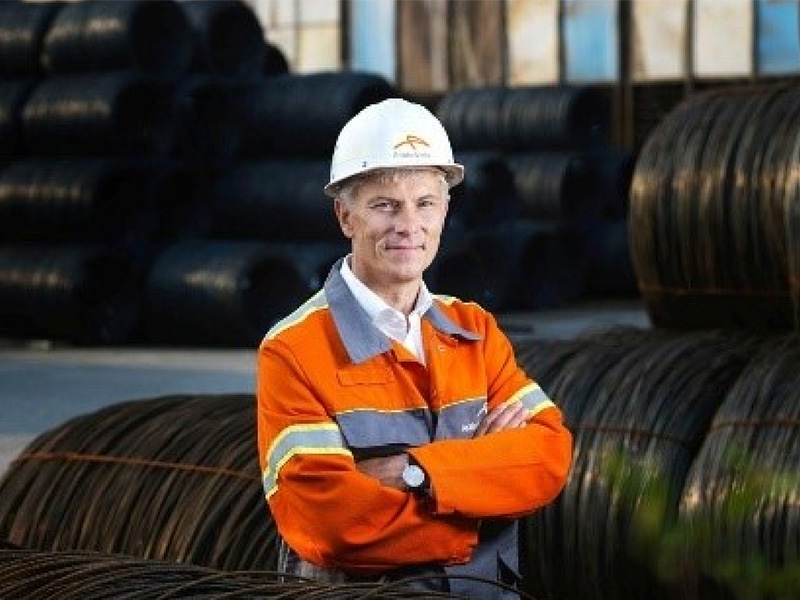